INDUSTRIAL NEWS
How to Reduce Waste in Acrylic Laser Cutting Projects
Acrylic laser cutting is a versatile and efficient method for creating precise designs and products. However, waste is a significant factor to consider, both for cost savings and environmental reasons. By implementing specific practices, you can reduce waste in your acrylic laser cutting projects. Here are some strategies to achieve efficient usage and minimal material waste with MYounglaser CO2 laser machines.
1. Optimize Design Layouts
When planning a laser cutting project, designing layouts to maximize material use is one of the most effective ways to reduce waste. Place multiple parts or designs close together to fit as many as possible on a single acrylic sheet. With precise layout planning, you can minimize scrap material.
Nesting Techniques: Using software for layout optimization, also known as “nesting,” is highly effective. Programs can automatically arrange parts to maximize material usage.
Design Prototyping: For intricate designs, prototype your layout on inexpensive materials first to avoid errors on the final acrylic sheet.
2. Select the Appropriate Acrylic Thickness
Choosing the right thickness of acrylic for your project can also minimize waste. Thicker sheets may not be necessary for certain designs, and they can lead to excess scrap if not cut efficiently.
Match Thickness to Function: Use thinner sheets for lightweight designs, and reserve thicker acrylic only when strength is needed.
Test Cutting with Scrap: Use leftover or scrap acrylic for testing settings and ensuring that your cut is accurate.
3. Use Efficient Cutting Paths
The path your CO2 laser takes can significantly impact both the cut quality and the amount of wasted material. Proper planning for the cutting path ensures less movement between cuts, which reduces time and excess laser exposure to the material.
Minimize Travel Distance: Arrange designs so that the laser cutter follows a continuous path with minimal empty travel distance.
Reduce Overlap and Double Cuts: Avoid redundant cuts or overlaps, as these can lead to inconsistent edges and additional waste.
4. Repurpose Offcuts and Scraps
Small pieces or offcuts that might normally be discarded can often be reused for other projects. Many intricate designs require smaller acrylic sections, making these leftover pieces perfect for future use.
Store Scrap Systematically: Organize and label scrap material by size and thickness for easy identification in future projects.
Incorporate Scraps in New Designs: For smaller components like keychains or ornaments, these offcuts can be ideal, helping you reduce waste significantly.
5. Optimize Power and Speed Settings
Setting the correct power and speed on your MYounglaser CO2 laser machine is essential to achieving clean cuts with minimal waste. Incorrect settings can lead to melting, charring, or misaligned cuts, resulting in unusable material.
- Test Different Settings: Conduct test cuts on scrap acrylic to find optimal speed and power combinations for each thickness.
- Use Preset Profiles: If available, use machine presets specific to acrylic cutting to maintain consistent results and reduce errors.
6. Maintain Your CO2 Laser Machine
Regular maintenance ensures that your CO2 laser machine performs accurately and efficiently. Properly calibrated machines produce cleaner cuts, reducing the chance of material wastage from re-cuts or mistakes.
- Clean Optics and Align Laser: Regularly cleaning lenses and mirrors, and keeping the laser aligned, results in more precise cuts and minimizes the need for repeat work.
- Replace Worn Parts: Components such as laser tubes and mirrors should be replaced as needed to prevent issues that might compromise cutting quality.
7. Recycle Acrylic Waste
Not all scrap material can be reused directly, but acrylic can often be recycled. Partnering with a recycling company that accepts acrylic can reduce your environmental impact.
Separate Waste for Recycling: Keep acrylic waste separate from other materials and store it for pickup or delivery to recycling centers.
Use Biodegradable Acrylic: For a more sustainable option, consider using biodegradable acrylic, which can break down more easily than traditional acrylic in disposal environments.
Reducing waste in acrylic laser cutting projects not only enhances cost-effectiveness but also demonstrates a commitment to environmental responsibility. By optimizing layouts, selecting suitable thickness, managing cutting paths, repurposing scraps, adjusting power settings, maintaining equipment, and recycling waste, you can greatly minimize material waste.
MYounglaser’s CO2 laser machines are designed to support precision and efficiency, making waste reduction achievable in every project. For high-quality machines that balance cutting precision with sustainable practices, MYounglaser offers reliable solutions.
Ready to Speak with One of Our Experts?
Getting started on any project can be daunting. Let us handle the technicalities so you can focus on bringing your designs to life.
Open the box; pull out your machine; and get to work. Whether you’re engraving on wood, leather, acrylic, or metal, just let us know your materials of choice, and we’ll find the perfect machine for your needs.
If you’re ready to upgrade your equipment, elevate your business, or simply unleash your creativity, we’re here to assist.
At Foshan Myoung Laser Technology Co., Ltd., established in 2012, we pride ourselves on integrating R&D, manufacturing, sales, and service to deliver top-notch laser solutions. Our range includes laser cutting machines, laser welding machines, laser marking machines, and industry-specific and automated laser equipment.
Got questions? Comments? Curious about our cutting-edge laser technology? Schedule a call with us today. We actually answer our phones and are here to help you every step of the way.
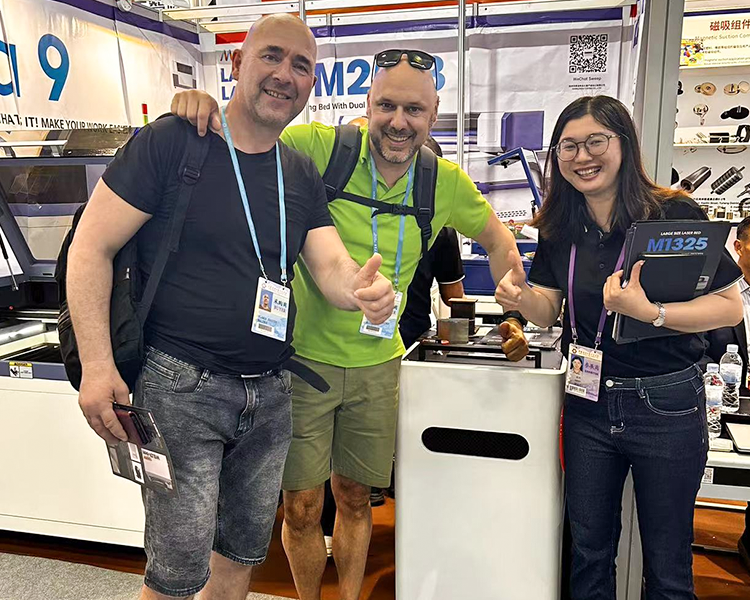
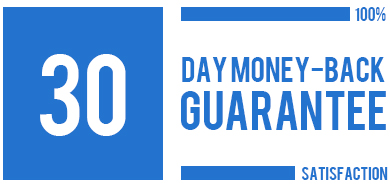
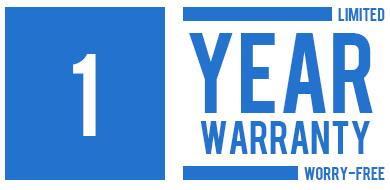
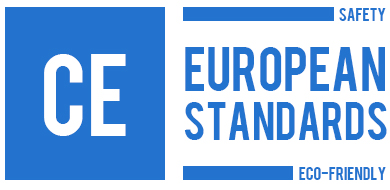