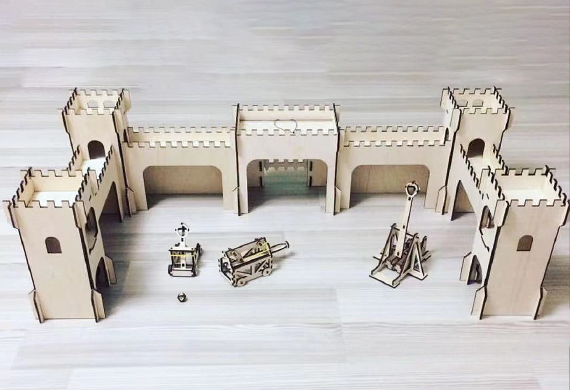
How to Define a High-Quality
INDUSTRIAL NEWS
When it comes to laser cutting machines, a high-quality CO2 laser cutter stands out as one of the best options available. With its versatility, precision, and efficiency, it has become a popular choice in various industries. However, defining what makes a CO2 laser cutter high-quality requires a closer look at its key features and capabilities.
First and foremost, a high-quality CO2 laser cutter should have a powerful laser source. The laser source determines the machine’s cutting ability and speed. A CO2 laser cutter with a high wattage ensures faster and more precise cutting, making it suitable for a wide range of materials, including wood, acrylic, fabric, and even metal.
Another crucial aspect of a high-quality CO2 laser cutter is its cutting bed size. The cutting bed should be spacious enough to accommodate different sizes of materials. This enables users to work on larger projects without the need for multiple setups or splicing. Additionally, a high-quality CO2 laser cutter should have a reliable and sturdy cutting bed that can withstand the heat generated during the cutting process.
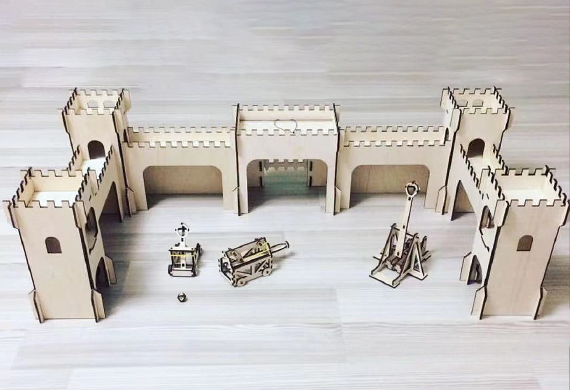
Precision is also a key factor in defining a high-quality CO2 laser cutter. The machine should be equipped with advanced motion control systems and high-precision components to ensure accurate and consistent cutting results. This includes features like auto-focus, which adjusts the laser’s focal length automatically, ensuring optimal cutting depth and quality.
Moreover, a high-quality CO2 laser cutter should provide users with a user-friendly interface and intuitive software. The interface should be easy to navigate, allowing users to control the machine’s settings, such as laser power and cutting speed, effortlessly. Additionally, the software should support various file formats and offer customization options, enabling users to create intricate designs and patterns.
Safety features are also crucial when defining a high-quality CO2 laser cutter. The machine should have safety measures in place, such as emergency stop buttons and protective enclosures, to ensure the well-being of operators. Additionally, it should have a reliable cooling system to prevent overheating during prolonged use.
Lastly, a high-quality CO2 laser cutter should come with excellent customer support and after-sales service. This includes providing comprehensive training and technical support to users, as well as offering warranties and maintenance services to ensure the longevity and efficiency of the machine.
In conclusion, a high-quality CO2 laser cutter can be defined by its powerful laser source, spacious cutting bed, precision, user-friendly interface, safety features, and reliable customer support. These key features and capabilities make it an ideal choice for various industries, where precision cutting and efficiency are paramount.