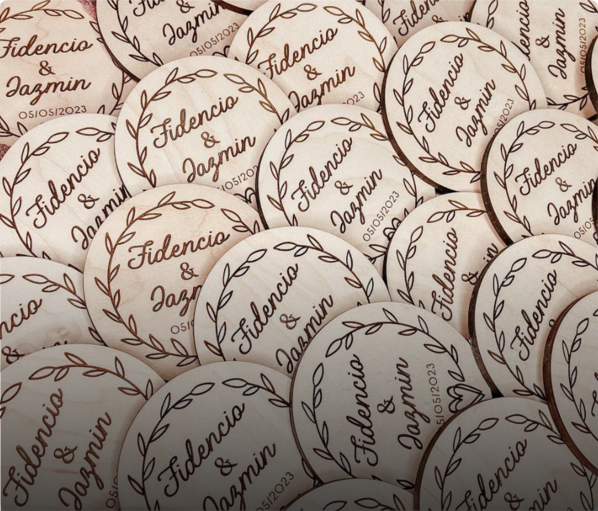
10 Creative Acrylic Laser Cutting Projects
INDUSTRIAL NEWS
10 Creative Acrylic Laser Cutting Projects
Acrylic is one of the most versatile materials for laser cutting, offering a balance of durability, precision, and aesthetic appeal. Here are 10 creative projects that you can explore using a CO2 laser machine like the ones from MYounglaser. Whether you’re an entrepreneur or a hobbyist, these projects offer the perfect canvas for creativity and profitability.
1. Custom Acrylic Signs
Acrylic signs are widely popular for businesses and home decor. With a CO2 laser machine, you can engrave logos, names, or intricate patterns onto acrylic sheets. The versatility of acrylic ensures that the signs are durable and visually striking.
2. Jewelry and Accessories
From custom earrings to bracelets and pendants, acrylic is a fantastic material for lightweight and stylish jewelry. Use colored or mirrored acrylic to make bold, unique designs.
3. Acrylic Light Panels
Create personalized light panels using clear or frosted acrylic. Engrave patterns or text, and combine with LED lighting for a stunning effect that is perfect for home decor or signage.
4. Acrylic Phone Stands
Design sleek and modern phone or tablet stands. With the precision of a CO2 laser machine, you can create intricate slots and support structures that perfectly fit electronic devices.
5. Laser-Cut Acrylic Clocks
Create a custom acrylic clock with intricate details and unique designs. You can cut both the clock frame and numbers using your laser machine, adding a personal touch to timekeeping.
6. Home Decor Items
From acrylic mirrors to photo frames, laser-cut acrylic can add elegance to any space. Use clear or colored acrylic sheets to create personalized decor items that reflect individual style.
7. Acrylic Awards and Trophies
Acrylic is often used in making professional awards and trophies. With laser engraving, you can personalize each award, adding names, logos, or intricate designs.
8. Acrylic Keychains
Acrylic keychains are a fun and simple way to create personalized items. These can be used for promotional materials, gifts, or souvenirs. Use your MYounglaser machine to cut complex shapes and engrave text.
9. Acrylic Display Stands
Retailers often need custom display stands for products. You can use acrylic to create sturdy and transparent stands that showcase products beautifully, whether it’s for cosmetics, gadgets, or art.
10. Acrylic Ornaments
For holidays or special events, laser-cut acrylic ornaments are a fantastic craft idea. You can design seasonal items like Christmas ornaments, wedding decor, or custom shapes for any occasion.
Why Use MYounglaser for Acrylic Cutting?
The MYounglaser Dura series machines are optimized for precision cutting and engraving on acrylic, offering advanced features such as:
- Japan Shinano motor and driver for high torque and precision
- Linear module guide rails for smooth and quiet operation
- High-quality laser tube and accessories for exceptional performance
- Flexible design that allows for engraving and cutting of both thin and thick acrylic materials.
These features make MYounglaser CO2 laser machines an excellent choice for those looking to create stunning acrylic projects with both ease and precision. If you’re ready to bring your designs to life, check out our machines for reliable and high-quality results.