INDUSTRIAL NEWS
The Principles and Features of Laser Cutting — Laser Knowledge Science
The Principles of Laser Cutting
Laser cutting is a technique that utilizes a high-energy-density laser beam to irradiate the workpiece. The material being irradiated quickly melts, vaporizes, burns, or reaches its ignition point. Simultaneously, the molten material is blown away by a high-speed gas flow that is coaxial with the laser beam. This process allows for precise and efficient cutting of a wide range of materials.
Basic Principle:
- Laser Generation: A laser is generated by stimulating laser-active material, such as CO2, Nd
, or fiber, to emit light.
- Beam Delivery: The laser beam is directed towards the workpiece through a series of mirrors or fiber optics.
- Material Interaction: When the laser beam strikes the material, it heats the material to its melting or vaporization point.
- Material Removal: A high-pressure assist gas (such as nitrogen, oxygen, or air) is used to expel the molten or vaporized material from the cutting area.
Key Features of Laser Cutting
- High Precision: Laser cutting offers extremely precise cuts, making it suitable for detailed and intricate designs. The laser beam can be precisely controlled to achieve a high level of accuracy.
- Smooth Cutting Edge: The cuts produced by laser cutting are clean and smooth, often requiring no further finishing. This is particularly advantageous in industries where the quality of the cut is crucial.
- Versatility: Laser cutting can be applied to a variety of materials, including metals, plastics, wood, and textiles. This versatility makes it a popular choice across different industries, from automotive to fashion.
- Minimal Heat-Affected Zone: Due to the focused nature of the laser beam, the heat-affected zone is minimal. This reduces the risk of material warping or damage near the cut area.
- High Speed: Laser cutting is a fast process compared to traditional cutting methods. This efficiency translates to increased productivity and reduced manufacturing time.
- Automation: Laser cutting machines can be easily integrated into automated production lines, enhancing overall efficiency and reducing labor costs.
- Non-contact Cutting: Since laser cutting is a non-contact process, there is no physical wear on the cutting tool. This extends the lifespan of the equipment and ensures consistent cutting quality over time.
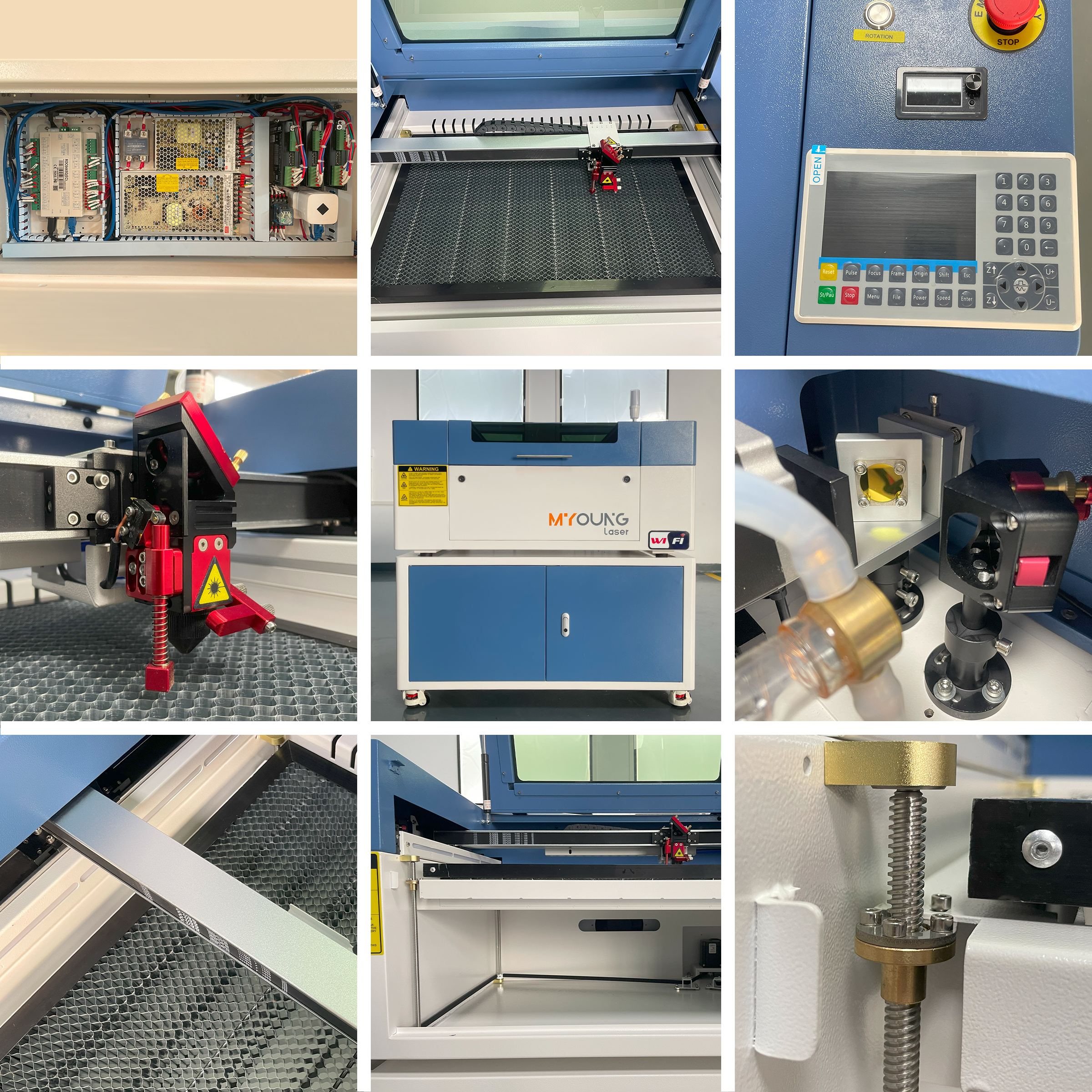
Applications of Laser Cutting
Laser cutting technology is used in a wide array of industries due to its precision, efficiency, and versatility:
- Manufacturing: Laser cutting is extensively used in the automotive, aerospace, and electronics industries for cutting and shaping metal and plastic components.
- Medical Devices: Precision and cleanliness of laser cutting make it ideal for producing medical devices and equipment.
- Signage and Advertising: Laser cutting is used to create detailed and customized signage from various materials.
- Textile Industry: Laser cutting allows for intricate patterns to be cut into fabrics with high precision and minimal fraying.
- Art and Jewelry: Artists and jewelers use laser cutting to create detailed designs and patterns in various materials.